We Started the Liquid Printing Revolution
Immersion Graphics of Columbus, Ga., made the outdoor industry take notice in the late 1990s when it introduced a radically new decorative transfer printing process called Final Finish® and applied it to shotguns and bow parts.
Today, companies around the world use this technology to boost sales, target niche markets, and add value to their products. It gives plastic motorcycle parts the appearance of metal and plain steering wheels the look of fine wood and leather. The process is so realistic that comparisons to the decorated product and the actual product leave the naked eye guessing.
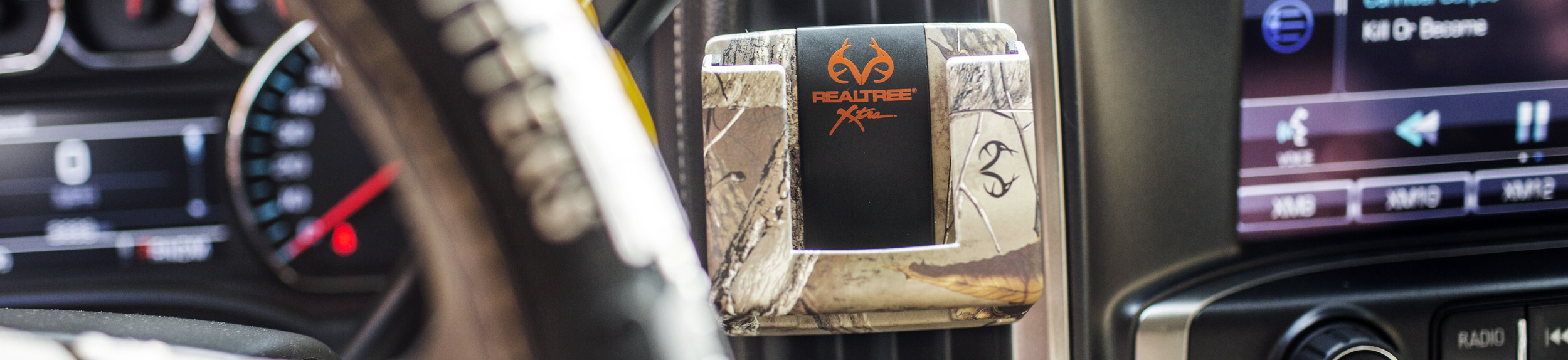
Who’s Decorating?
Companies including Nikon, Cabela’s, Chrysler, Timex and Yamaha use our technology to boost sales. Shouldn’t you?
At first, a select few in the outdoor industry embraced Final Finish®. Parts for bows, coolers, rifles and even ATVs, were dipped in a camouflage pattern, assembled and sold. When demand increased, those thinking outside the box tested the waters — literally. Today, caskets, laptops, automotive interiors, cell phones, hockey masks and home accessories are enhanced by the process. Water transfer technology gives companies including Nikon, GM, Chrysler, Cabela’s, Timex, Thompson/Center, Bear, Motorola, Beretta, Benelli, Yamaha, KMM and Suzuki a competitive edge by offering added value and eye appeal.
Where It’s Done
Companies perform the decorative process in their facilities or with a licensed specialist. Immersion Graphics provides equipment and technical support, and ships its film when and where it is needed. In addition to Immersion’s extensive list of licensees in North America, international licensees include customers in Japan, Portugal, Italy, Turkey, England, Mexico, Taiwan, Spain and Canada. Immersion also provides the Final Finish® product to One Source Automotive in Asia, which services Toyota, Nissan, Honda, Mazda, Subaru, Mitsubishi, Daihatsu and Suzuki.

Where It's Done